進行:ゴンドラのサイズ種のヒアリングから開始
アイリスオーヤマ様の商品が陳列されるホームセンターでは、店舗規模などに応じて商品陳列棚(ゴンドラ)の横幅が1200mmと900mmの2種が混在していることが判明しました。どちらもメジャーなゴンドラの定形サイズです。
2種とはいえ、同じ内容を示す2種のトップボードを製造となると、コスト以外にも付随する手間(工数)が派生していることが見えてまいりました。
- トップボード2種をデザインする工数
- 2種分製造する工数
- 梱包する資材2種分の手配工数
- 配送先を間違いないように手配する工数
パネル1枚のコスト縮減も大事ですが、調整が必要な運用上の手間の縮減も大事です。やはり製造するトップボードは1種にし、加工で2種のゴンドラへの対応がリーズナブルと判断、可変型トップボードをご提案いたしました。
可変型トップボードは、ボードの表面900mm位置にスリット(両面)を入れ、所謂「手でも割れる※断面の美粧性をを追求される場合は、カッターを用いての断裁をおすすめいたします」仕様のトップボードです。
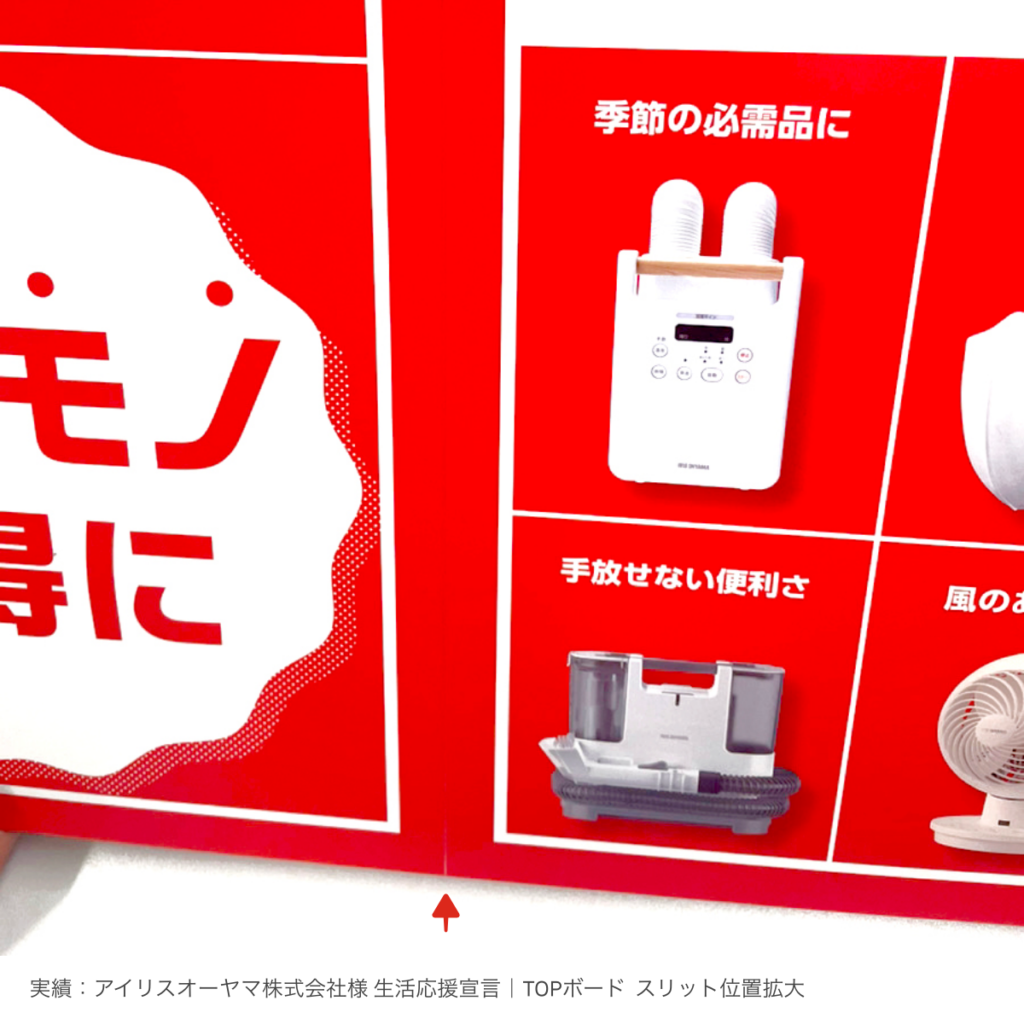
成果:制作物を1種にしたことで、コストと手間の縮減に成功
制作物を1種にすることでそれまで2種製造にかかっていたコストと工数が解消しました。とりわけ販促ツールご担当者様の工数を軽減、他の業務に時間を割ける状況をご支援できたこともアウトカム(成果)として挙げさせていただきます。
発見:カスタマイズが発生する場所の見極めが重要
ゴンドラサイズが違うので、掲示するPOPのサイズを変える。POPの企画、設計、デザイン、製造、梱包、配送、掲示の流れの中で、上流工程の「設計」工程から2種、梱包資材も2種、配送手配も2種分かけるよりも「掲示」工程で2種選択可能な仕様にするだけで、上流工程の工数を縮減できます。
どこの工程で何を変えればよりコストと工数が縮減できるかが重要なのだと考えます。当社は日々そんな問題/課題と向き合ってお客様の販促活動を支援させていただいております。ぜひお気軽に問題/課題をお聴かせください。意外と第3者の目から工数とコスト縮減のきっかけが見つかるかもしれません。
この案件で取り扱ったベース商品
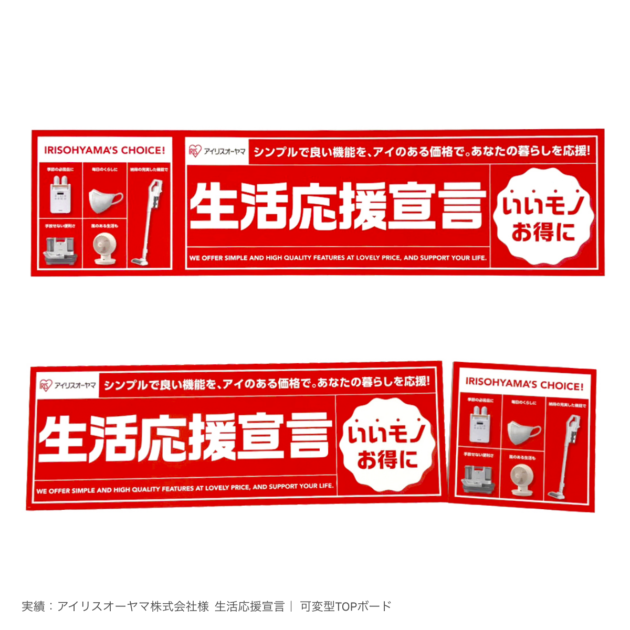